CO’LaB 3D imprime sa marque aux HCL
C’est un service des HCL qui casse les codes. Par son activité d’abord : l’impression 3D. Si aujourd’hui on envoie dans l’espace des fusées en métal imprimées en 3D*, la création de pièces en volume est encore rare au sein des établissements hospitaliers. « Nous avons été parmi les premiers à internaliser le savoir-faire et sommes la seule plateforme hospitalière en France à être certifiée ISO 13485 », explique Peggy Leplat-Bonnevialle, dynamique coordinatrice de CO’Lab 3D.
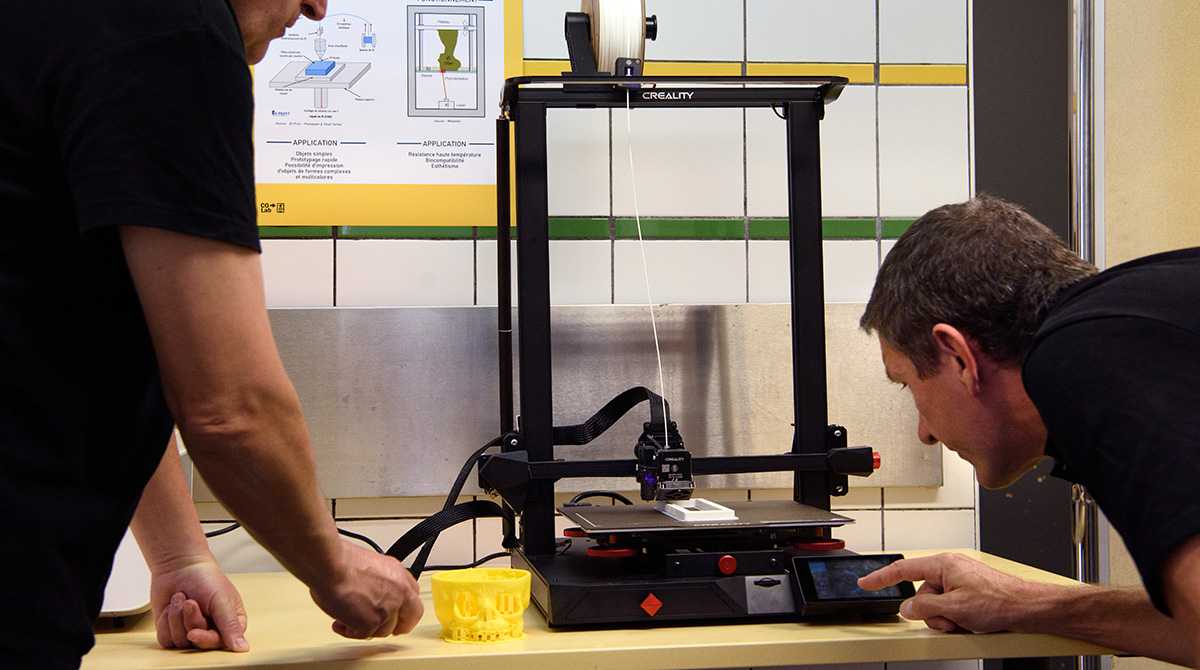
Cette plateforme de fabrication additive est née d'un partenariat avec l'Insa Lyon à l'issue de la première vague Covid. Aujourd’hui, ses 23 imprimantes sont installées au rez-de-chaussée d’un bâtiment du site de Lacassagne, dans un ancien restaurant-self transformé en atelier géant, où l’on croise toutes sortes d’objets en plastique coloré — une oreille, des médicaments, un clitoris, un crâne… — et des bureaux-établis accueillant des pinces, des bobines de fils chamarrés, des gants, un mini-chalumeau, une brosse à dents ou encore des blocs-notes griffonnés de formules étranges.
Faire bonne impression
Ingénieure de formation, également chargée de mission innovation & partenariat au sein des HCL, Peggy Leplat-Bonnevialle précise : « Nous sommes un service à disposition de toute la communauté, qui fonctionne sur un mode agile, inspiré de l’holacratie**, avec une ambition claire et partagée. Notre innovation est aussi managériale. » Une singularité récompensée le 8 juin dernier, au niveau national, par le trophée Innovation Team Best Practice 2023, un prix qui célèbre les équipes partageant « une même vision, prenant l’initiative, sortant de la routine pour réaliser leurs projets et combinant leurs talents »***.
Fonctionnelle depuis 2020, CO’Lab 3D fédère, sur la base du volontariat, douze professionnels de santé épaulés par quatre enseignants Insa (Institut national des sciences appliquées). Tous possèdent des expertises complémentaires tout en ayant des missions par ailleurs. « Au début il y a eu un appel à des directions ciblées et j’ai eu envie de participer à cette aventure », explique Sylvain Gouttard, ingénieur en imagerie médicale, qui donne plusieurs heures par mois à ce service « support » atypique. Sa spécialité : le traitement des images dont il extrait une zone qui sera ensuite modélisée, puis transformée en fichier imprimable. De part et d’autre de son écran qui affiche un crâne en 3D, deux gros cubes noirs ronronnent discrètement, signe que derrière la vitre sombre, un objet est en train de prendre forme.
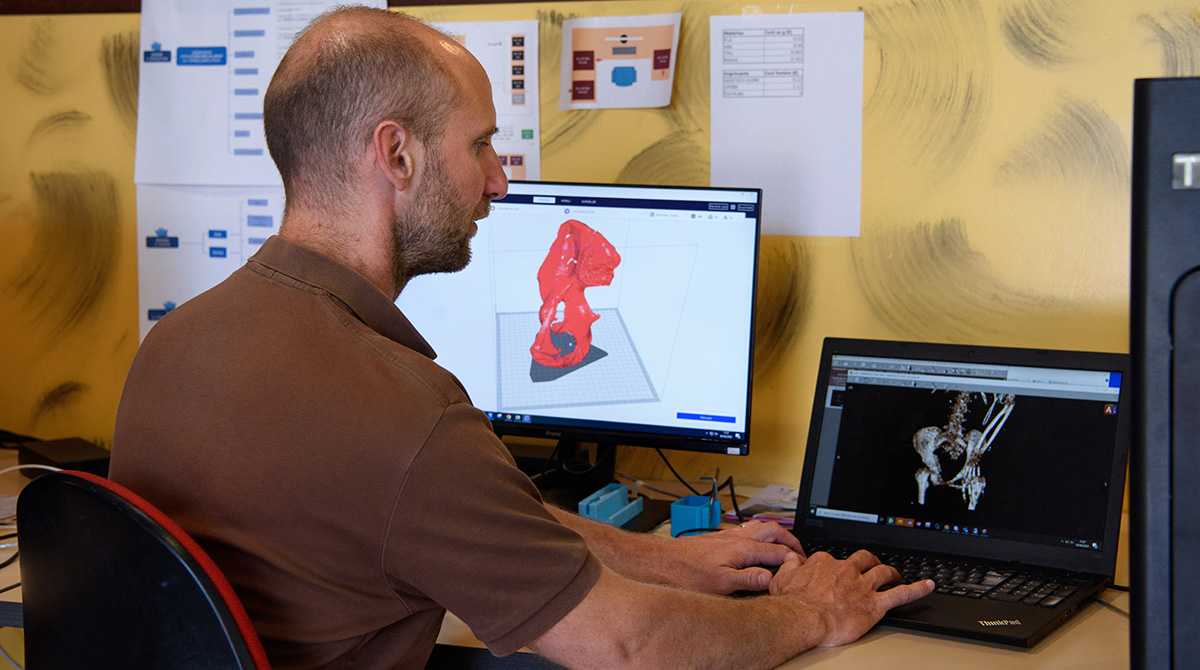
« Nous sommes en train de concevoir un modèle anatomique pour de la planification chirurgicale », indique Mélia Virely, ingénieure impression 3D. D’autres modèles imprimés sont présentés tels qu’une oreille en résine fabriquée à la demande d’un chirurgien ORL pour servir de modèle dans une chirurgie réparatrice, un cerveau avec des hémisphères qui peuvent se diviser pour expliquer la prise en charge de l’épilepsie aux patients, un clitoris taille réelle, imprimé en TPU (un élastomère thermoplastique doté d'une grande élasticité, NDLR) pour un médecin conseil en PMI ou encore un porte-stylo imaginé par un ergothérapeute pour des patients qui ont perdu la fonction de pince au niveau de la main.
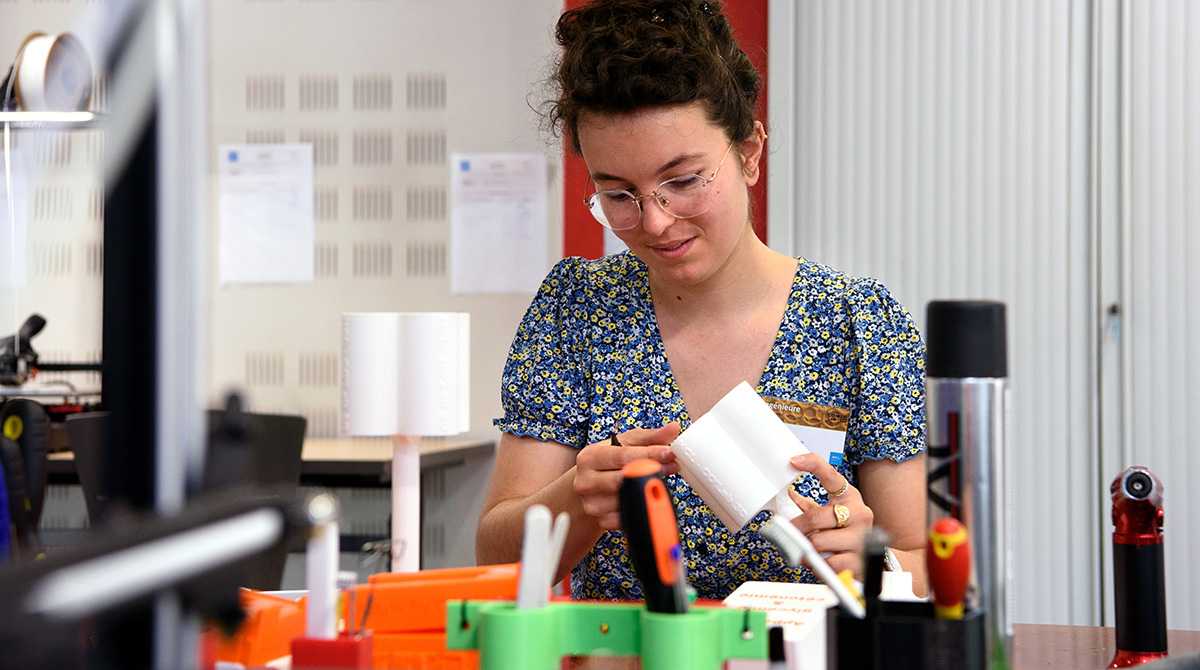
« Avec et pour »
Seule permanente de l’équipe, Mélia accueille les personnels des HCL, techniciens de laboratoire, administratifs, personnels de restauration ou encore soignants, rencontrant un problème pour lequel il n’existe pas de réponse. « Nous les aidons à caractériser leur besoin, puis concevons un prototype que nous affinons en fonction de leurs retours. » En trois ans d’existence, la plateforme a ainsi coconçu plus de deux cents objets, essentiellement des aides techniques pour personnes en situation de handicap, des pièces détachées, ou des objets sur mesure.

des pièces détachées, ou encore des objets sur mesure.
« Nous travaillons avec les professionnels de santé, pour les patients et ne fabriquons que des objets personnalisés qui n’existent pas dans le commerce », résume Peggy Leplat-Bonnevialle. Comme cette coque de protection avec ancrage pour appareil d’échographie portatif pour laquelle les a sollicités Éric Benignus, infirmier technique au Samu. « Nous avions beaucoup de casse sur les appareils et le constructeur ne proposait rien pour les protéger hormis une valise rigide lourde, difficile à emporter en intervention. J’ai interrogé CO’Lab 3D, qui a modélisé le concept et produit le premier prototype », se félicite-t-il en observant le ballet de la buse qui, patiemment, dépose des fils fondus jusqu’à créer, en trente-cinq heures environ, la coque qui sera fabriquée à une dizaine d’exemplaires.
Habitué de la plateforme qu’il avait déjà sollicitée pour un support de câble pour scope de saturation d’oxygène, il sait qu’à la clé son service va faire de substantielles économies : « Chaque appareil coûte plus de 25 000 euros et la moindre réparation 8 000 euros, là où le prix d’une coque imprimée, intégrant la matière première, la conception et la main d’œuvre, est d’environ 100 euros. »
Près de 500 000 euros de « non-dépenses »
Une prestation qui ne sera pas facturée à son service, CO’Lab 3D préférant comptabiliser les non-dépenses. « En trois ans d’existence, nous avons déjà fait économiser de l’ordre de 500 000 euros aux HCL », constate Peggy Leplat-Bonnevialle.
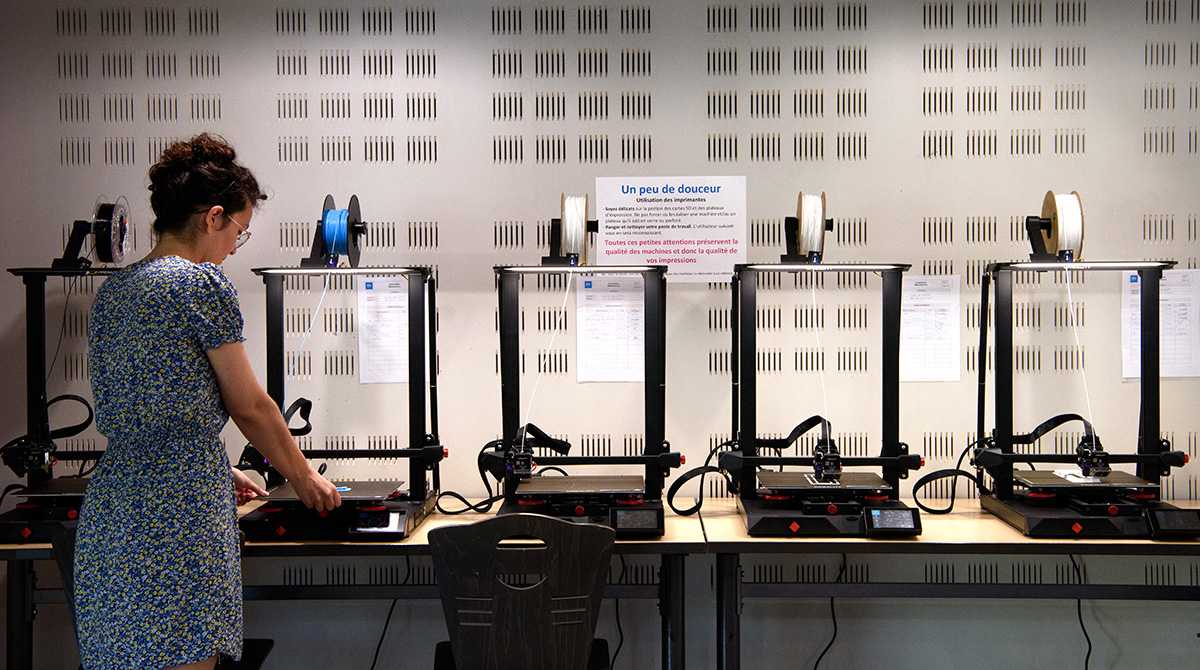
Un des objectifs de 2023 pour consolider le modèle est de développer des prestations externes, comme celle pressentie avec un établissement de santé à Paris, intéressé par des boîtes pour ampoules de stupéfiants initialement fabriquées par la plateforme à la demande de Lyon Sud. De nouveaux débouchés qui incitent les équipes à déposer des brevets ou des enveloppes Soleau. Comme pour Ipefix, un fixateur de pédales innovant et breveté développé avec le Pr Mathieu Pioche, gastroentérologue, qui permet de fixer au sol les différentes pédales des outils utilisés lors de procédures endoscopiques.
Seule plateforme hospitalière d’impression 3D de la région, CO’Lab 3D propose également des modules de formation pour aider les établissements à développer leur propre structure d’impression 3D. Une montée en charge qui ne perturbe en rien le ronron de l’imprimante qui poursuit son patient travail sur la coque de protection. L’écran indique que dans une heure et demie, elle sera disponible. Impressionnant !
*En mars dernier, aux États-Unis, la toute première fusée, dont la majorité de la structure ainsi que les moteurs ont été fabriqués par impression 3D, en métal, a décollé avec succès.
**Concept de management reposant sur l’intelligence collective, la motivation et le sens de l’autonomie des salariés.
***Le trophée Innovation Team Best Practice est décerné par le Club de Paris des directeurs de l’innovation, l’Institut européen des stratégies créatives et d’innovation (ESCI) , l’École d'économie de l'université Paris 1 Panthéon- Sorbonne et la Chaire ETI - IAE Paris Sorbonne School.